We’re talking about an eSurf here, there is a lot of friction on the water so I’m skeptical of your claimed 2hr battery life no matter how well you design the hydrodynamics.
Commercial batteries can’t perform magic, they are typically using the same, or worse cells than I’m planning on using. Specifically, the Molicel P45B cells are among the best on the market today, and no commercial battery has secret battery technology that vastly surpasses it.
There is a nice spreadsheet floating around called ‘eFoil battery calculator’ that I’ve used to estimate a realistic runtime. The nice thing about it is that it provides an estimate in terms of how much energy is required, so it’s independent of how you get there (hydrodynamic improvement, motor improvements, etc).
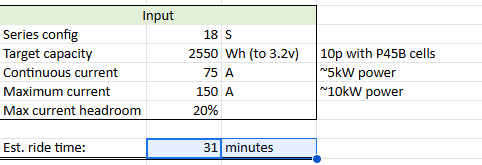
This is a screenshot of my current estimates. There are really only two variables to play with that make a difference in runtime, the target capacity and the estimated continuous current required (which is affected by hydrodynamics and other factors).
For size/weight reasons, a 18s10p pack of 21700’s is about as big as you can go on an eSurf. The 180 cells alone will weight ~30lbs and much more once you add the bus bars, BMS, wiring, case, etc. So if you try to achieve 2hr by increasing capacity, you would need ~18s36p, which would be completely impractical from a size/weight perspective (well over 100lbs for the complete battery).
So that leaves continuous current as the only viable parameter to increase runtime. I’m currently estimating ~5kW of battery power (75A at 18s) required for continuous operation (on average). A typical commercial eSurf has between a 10-20kW motor, so this seems reasonable, but feel free to provide justification for why it’s not a good estimate. I admittedly just spitballed it, but for reference, to get to 2hr runtime we’d have to achieve ~1.3kW continuous power, which wouldn’t justify the large motors typically found in eSurfboards, so I don’t think it’s realistic.
TLDR, I agree my board shape and motor setup aren’t expertly optimized. However, putting in a lot of effort on optimizing the shape/motor/nozzle/impeller is never going to give a 4x reduction in required power (10-20% improvement is more realistic).
In conclusion, if I’ve made some incorrect assumptions or mistakes, by all means point them out, however it’s not helpful to make wild assertions without providing any details to back it up. If you are in fact an expert in hydrodynamics or impeller design, please provide specific suggestions, simulation results, detailed calculations, etc. Otherwise, please keep the baseless assertions to a minimum.